A newly printed paper from Newmont’s Calen Beaune goes some solution to showcasing what it takes to set an underground mine up successfully and effectively for battery-electric haulage, beginning with battery cost bay location.
His paper, ‘Plan vs Precise: A comparability of electrical haulage truck cost bay places (printed right here),’ particulars a part of the battery-electric journey of the Brucejack gold mine in British Columbia, Canada.
Whereas many would assume the journey began in October 2020 when the primary of eight Sandvik Z50 electrical haul vehicles arrived, it’s clear from Beaune’s paper that the planning for these autos commenced a very long time earlier than that.
“Preliminary planning relied on a simulation mannequin that forecast charging wants and optimised fleet sizes over a ten-year interval (2022-2033),” Beaune, Brucejack Mine Coordinator, stated. “Nevertheless, a number of unexpected challenges led to deviations from the unique structure, together with energy availability, geotechnical constraints and operational issues associated to battery administration.”
Plan vs Precise
Brucejack is an underground gold mine that makes use of a long-hole stoping mining methodology, with a mean of three,000-4,000 t/d of ore processed.
Supplies are trucked from the stope location to a central tipping level on the underground crusher after which conveyed to floor.
The mine extends from 1,500 metres above sea degree (masl) to 960 masl with a central ramp connecting every degree. A satellite tv for pc zone (West Zone, WZ) is linked underground however doesn’t but assist stoping actions.
The Sandvik Z50, in the meantime, is a 50-t payload battery-electric truck, and the predecessor to Sandvik’s TH550B vehicles. The primary truck arrived on web site in October 2020, with subsequent vehicles arriving roughly each 4-5 months. Brucejack was an early adopter of this know-how, serving as an preliminary – however not the one – location for the event of the Z50.
Cost bays to assist the arrival of every addition to the fleet had been bolted onto the design: a course of that developed as the corporate learnt extra concerning the realities of working this increasing fleet.
Brucejack performed a simulation examine to raised perceive the optimum structure of charging infrastructure to assist implementation of a fully-electric haulage fleet, with this examine specializing in establishing the haulage profile as per the mine plan and growing an obligation cycle to anticipate battery discharge charges.
“The examine recognized the situation of charging infrastructure and optimised the fleet dimension to fulfill manufacturing calls for,” Beaune stated.
An “Area mannequin” – based mostly on manufacturing planning from 2021 to 2033 – resulted within the choice of 4 places for the cost bays, noting that the very best trafficked space might require a couple of cost bay. The mannequin additionally calculated battery swaps at every location for durations overlaying 2022-2027.
“Battery swapping places had been chosen based mostly on the very best travelled areas with secondary bays barely decrease within the mine to scale back the chance of operating out of battery cost on decrease ranges,” Beaune clarified.
As these two figures beneath present, the deliberate cost bay places and the precise structure differed considerably, with Beaune explaining this was a results of “unpredicted issues that brought on deviation from the preliminary plan.”
Certainly one of these was a disconnection between {the electrical} plan related to the lifetime of mine (LoM) plan and the realities of working the incoming Z50 vehicles.
“Whereas substations had been ordered prematurely – as required for degree growth and cost bay wants – their placement and capability weren’t within the Z50 challenge constitution, and places weren’t cemented into the LoM plan for capital infrastructure and placement designation,” Beaune stated. “Additional, a misjudged assumption on cost bay design prices required plans to be enacted, which lowered capital by utilising present growth.”
The unique challenge constitution additionally underestimated the capital growth required for the cost bay design and extra cables required to attach the cost bays to the load centre, in response to Beaune, whereas the geotechnical assist (cable bolts) for the span had been additionally underbudgeted.
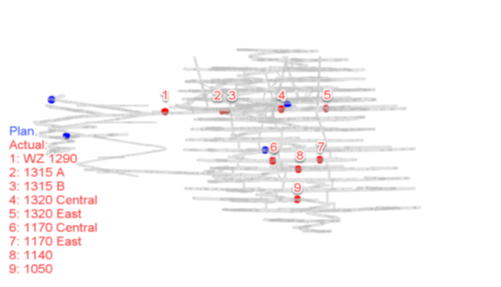
The unique plan known as for a single charging bay to offer a back-up for operators on 1200 Stage who didn’t have enough battery life to make a loaded journey from the underside of the mine to the tipple, in response to Beaune, but, when making the choice on subsequent bays, extra charging bays had been put in to make sure operators had quite a few choices to recharge within the decrease mine.
“Detailed battery administration planning for vehicles was largely an unknown on the time of design, and on-site operator issues centred round vehicles hauling from the bottom elements of the mine – requiring extra charging bays,” he added, explaining the relevance of this concern has confirmed troublesome to measure as a result of operators rarely-to-never-run-out of battery energy.
A number of developments have aided this decision-making course of for the reason that first autos arrived in 2020, in response to Beaune.
The primary bays had been designed based mostly on the enter and recommendation of the unique gear producer, Artisan with minimal equipment. Within the years since Sandvik’s acquisition of Artisan, the advised necessities for cost bays have elevated to incorporate:
- Air flow – ideally in a return airway in case of unlikely battery cell-venting;
- Comparatively dry- and dust-free areas;
- Cable covers or festoons – alongside cranes for cable motion;
- Concrete flooring for lowered upkeep and improved operator security;
- Drift dimensions 2 m wider than beforehand really useful (10 m vs 8 m); and
- Shotcrete charging space again over complete charging space
The extra equipment have benefit because the alternate options have actualised harm and incidents, in response to Beaune.
For battery administration planning, vehicles are assigned to a devoted cost bay, Beaune explains, which is dealt with on a shift-by-shift foundation through the use of vehicles related to cost bays nearest to the truck’s operational space. Nevertheless, given the unfold of the mine and the cost bays, there are situations the place a truck should make an empty journey to cost batteries. This reality inspired spacing bays all through the mine to perform as regional chargers for these stopes, however using 2-4 vehicles per stope ends in vehicles travelling farther to alter batteries, including to the cycle time.
“This downside is addressed by way of a program to hot-swap batteries by means of a dispatcher, who can direct vehicles to the closest absolutely charged battery and procure extra rigour and oversight on the method to drive effectivity,” Beaune defined.
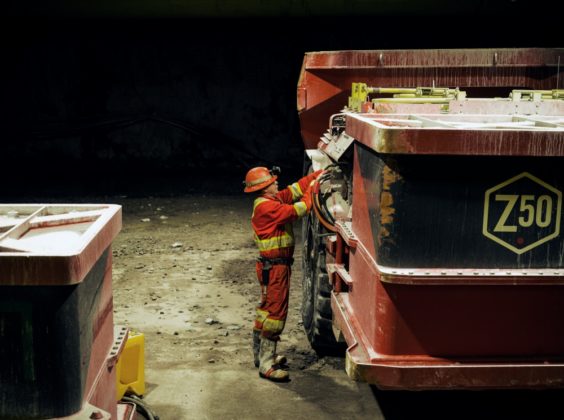
The addition of cost bays within the decrease mine was additionally pushed by a scarcity of obtainable areas within the centre to put them. A part of that is as a result of density of stopes on this space, whereas half is restricted by a scarcity of high-density orebody definition at a granular degree – extra definition drilling is required to substantiate an space is uneconomic to mine earlier than fastened infrastructure is put in, with drilling tending to concentrate on increasing the useful resource in excessive potential areas.
Unique cost bay designs had been located close to the footwall drive, nonetheless constructive ore outcomes introduced stoping to the intersection in most areas. Due to this fact, cost bays had been located farther into ranges, rising the time wanted for battery swaps.
The structure variations of every bay additionally include positives and negatives – there are alternatives to enhance security, value, upkeep and productiveness within the present designs.
“Looking back, a centralised charging space with all batteries – save for a singular low-mine backup – could be extra operationally efficient,” Beaune stated. “Wanting ahead, the location is evaluating cell cost bays to enhance flexibility and adaptableness to a altering mine plan.”
Typical shifts have averaged two battery swaps per truck per 10-hour shift.
Different operational modifications
The Z50 adoption required an growth in drift widths, from 4.5 m x 4.5 m to five.5 m x 5.5 m averages, whereas retaining the smaller Cat AD30 vehicles for historic areas. Truck load-out top additionally elevated to six.5 m. “These challenges are related to the improve in any gear and have brought on minimal points throughout transition,” Beaune defined.
A comparability of the outgoing fleet of Cat AD30s with the incoming fleet of Z50s confirmed that Brucejack realized a 64% t*km improve, with the effectivity acquire reaffirming the choice to improve the fleet to electrical choices, Beaune remarked.
Essentially the most difficult operational and design difficulty current entails truck dumping places, which requires a 7 m excessive again to soundly accommodate the 6.52 m mattress top, he famous. Ore-surge remucks on the crusher had been expanded by benching, with out water flooding points.
On-level remucks, nonetheless, have confirmed harder to plan as a result of the situation wanted for underground waste dumped from vehicles is usually sporadic.
This has lowered the effectivity of underground waste deposition however not halted it, Beaune stated.
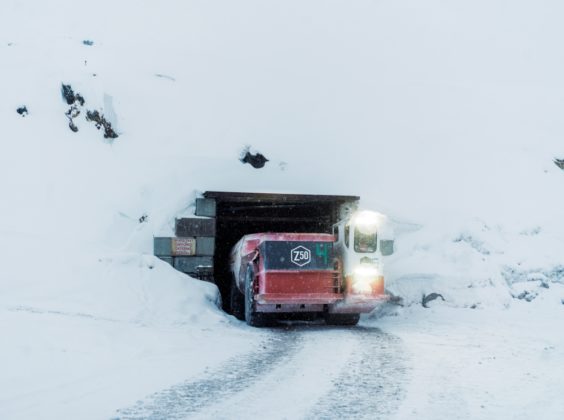
Structured strategy
For the cost bay design implementation to achieve success, a structured challenge administration strategy is required, in response to Beaune.
He says a devoted Tasks Supervisor is required to supervise planning, funding allocation and long-term infrastructure growth. Complete feasibility research and pilot implementations are additionally required earlier than full-scale deployment.
On prime of this, a transparent governance construction to make sure all technical, monetary and operational issues had been addressed prematurely would show extraordinarily helpful to any deliberate rollout. He additionally urged different mine operators to hold out proactive stakeholder engagement to align the engineering, operations and finance groups from the beginning.
Lastly, strong coaching and data switch packages would guarantee personnel understood system capabilities and limitations, aiding operational effectiveness.
Difficult and rewarding
The combination of electrical haul vehicles on the mine has confirmed to be each a difficult and rewarding course of, underscoring the complexities of implementing new applied sciences in underground mining operations, Beaune says.
Regardless of the aforementioned setbacks, the challenge has offered helpful insights into necessities and limitations of electrical car infrastructure within the mining sector. The addition of a number of charging bays, the reassessment of battery administration protocols and the continual refinement of design standards have resulted in a extra resilient and environment friendly charging system.
“Importantly, the teachings discovered spotlight the necessity for shut collaboration between gear producers, mine planners and challenge managers to make sure that infrastructure necessities are absolutely understood and built-in from the outset,” he stated.
The Brucejack expertise serves as a case examine for future underground mining tasks adopting electrical haulage methods, emphasising the significance of thorough planning, flexibility in execution and ongoing challenge administration to handle the evolving challenges of bold technological transitions.
Beaune concluded: “Because the mining business continues to maneuver towards sustainable, electrified options, the insights gained at Brucejack can be invaluable in shaping the way forward for underground electrical car infrastructure.”
All photographs used on this article had been provided by Sandvik Mining and Rock Options and must be credited to photographer Adam Lach